AA Brite 24/7 is located in Tucson, Arizona, and we put local exterior stucco into one of six categories:
The six most common types of exterior stucco include:
- Smooth Stucco Texture
- Sanded Stucco Texture
- Sprayed Cement Stucco
- Spanish Lace Stucco
- Tex Coating Stucco
- Synthetic Sprayed Stucco
Variations Within the Categories
Within each of these categories, there will be quite a bit of variation in workmanship, which affects the look and also the likelihood that patches can be applied without looking like patches. As another contractor I know says, “Great original stucco workmanship is easy to patch and paint; poor workmanship is a pain forever more.”
1) Smooth Stucco Texture
Advantages: Considered the most elegant looking by many people
Disadvantages: The walls almost always end up wavy with the framing and Styrofoam showing through. Cracks are difficult to repair and highly visible. Many of the cracks will be horizontal or vertical, which means two things. A) The stucco isn’t the problem; something under the stucco is moving and causing the crack. And. B) The crack is coming back.
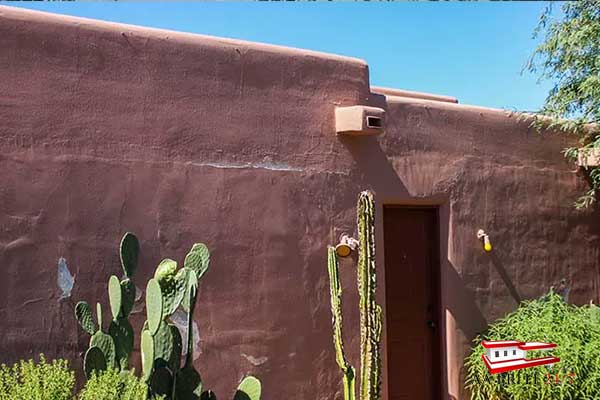
When well done, smooth stucco is often considered the most elegant looking. The mansion pictured on my main web page and below has a smooth stucco finish, and it looks great. However, smooth stucco comes at a price. The smoother and flatter a surface, the more it shows any defect or variation – and all walls have some waves and variations. Think of a shiny clean glass table with three grains of sand on it. The three grains of sand (read small defects) stand out so much because the table is smooth. It’s also the most difficult stucco to patch. Again think of trying to glue together a broken glass table without having any witness lines or scars, even after it’s painted. Though we repair it, it’s fairly difficult to do.
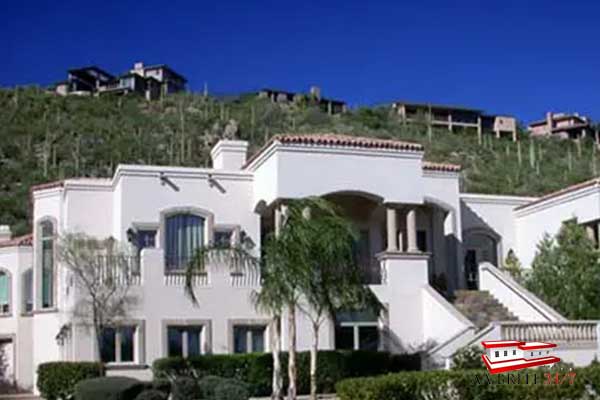
Well-done original flat stucco will only require minor crack repairs. With well-done stucco, the building will not look like a zebra when the prep work is finished, and it’s ready to be repainted since only a spot here or there was patched. As you slide down further in the quality of the original construction, the building will be more and more striped with repair work. When it looks like a zebra prior to painting, then some of the patchwork is going to show. For cases like this, there is only one other option, and that’s to re-stucco the exterior – which can cost ten to thirty thousand dollars.
[ Updated July 2nd, 2020] For the past ten years or so, I’ve had the smooth stucco information on my website. Since then, I’ve yet to see a single flat stucco house that didn’t have a lot of cracks in it. My opinion has changed some. I believe flat stucco homes can look great from a distance, but I don’t think one can stay looking great to a painter or anyone else with an eye for detail for over a year. They will crack, and if premium paint is used, they will all look wavy. If you have or know of non-cracked flat stucco that’s over a few years old, I’d love to hear from you and to see the house. I could write a book on this topic, but the number of flat stucco homes in my area is under one percent. If you need more information, please call me]
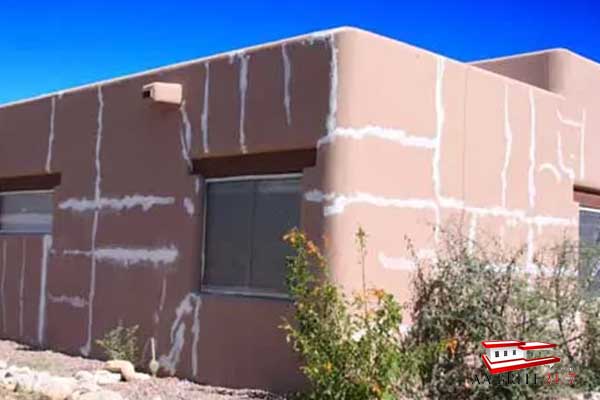
The photo above is of a home that could have been built better. It appears the foam backing is moving under the stucco, and there are quite a few waves. If a like-new finish is desired, then the correct answer is to entirely re-stucco the home. Since variations and defects are so visible on this stucco type, most builders avoid using it.
When cracks are perfectly horizontal or vertical, this is also an indication the materials under the stucco are moving. Cracks don’t naturally occur in straight lines. Looking at this picture, you can almost count the pieces of plywood and foam under the stucco – based on the way it’s cracking.
2) Sanded Stucco Texture
Advantages: Considered elegant looking and gives the home a soft feel.
Disadvantages: If there are air voids or the texture comes out sharp, it is difficult to patch.
Sanded stucco is much more common than smooth, and it’s a little more forgiving to work with. The texture created by the sand on the wall helps hide any waves or joints by camouflaging them. The key word being “helps.” Though it’s better than smooth from a repair point of view, it is still fairly difficult to patch without scars or spotting. Something working against whoever is doing the patching is the short height of the texture. Sanded stucco repairs are messed up by the inexperienced fairly frequently, with the most common mistake being caulk is applied directly to the crack and then left to dry as is. The resulting lines are called “scars,” and the big ones look terrible! See the Photo below of the homeowner’s repair.
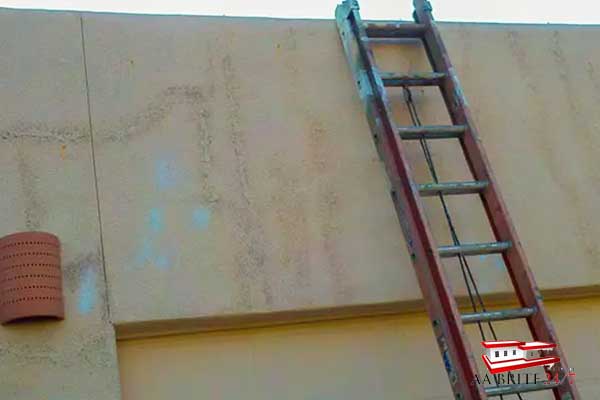
As a side note and according to my better half, when the addition is finished at my home, the existing exterior walls will be finished with a sanded stucco texture. We have adobe block now, and she wants sanded stucco for its soft and elegant look. Stuccoing after the addition is complete will also give the appearance that the house and additions were all built simultaneously. But back to the main topic.
Depending on the quality of the material and the craftsmanship, sanded stucco has a number of different looks.
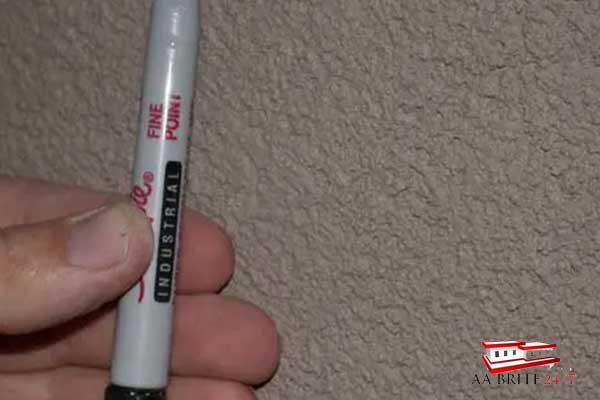
This is as good as it gets. There are almost no air bubbles, and getting the paint to laminate and waterproof the surface is not a problem.
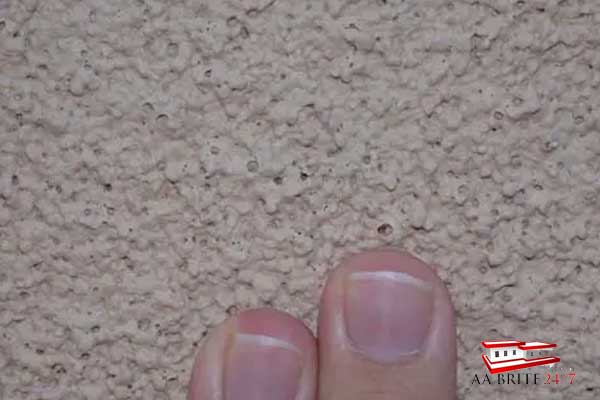
The stucco has quite a few open pores, and this is an intermediate-level paint job as a result of the extra work required to minimize the shadowing. Shadowing is when you see darker colors of the open air pockets when looking at the stucco from the side.
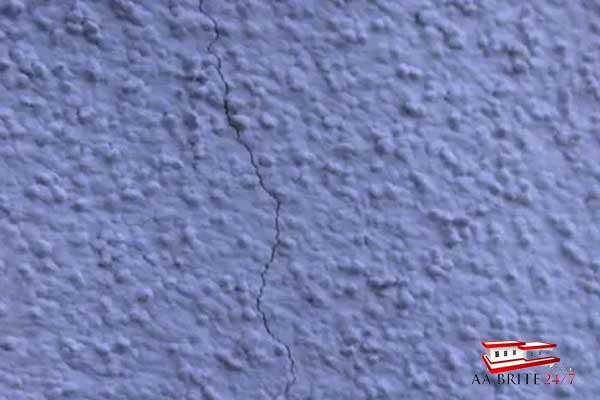
An older stucco with small grains of sand. Notice how the texture is soft (not pointed or really lumpy). The crack is a minor problem and can be filled in without scarring prior to or during painting. Paint and caulk are similar materials, and by forcing paint down into narrow cracks, they will not return unless there is movement of the stucco.
3) Sprayed Cement Stucco Repair
For conversational purposes “sprayed cement stucco” is only concrete stucco which was left alone after spraying. Its texture could be compared to thousands upon thousands of miniature volcanoes which come to sharp points. This texture can be quickly sprayed on and its biggest advantage is the texture helps hide defects and variations of the concrete blocks it is usually sprayed over.
Advantages: Applies fast. Can be used to blend in new and old construction.
Disadvantages: Sharp texture. Texture varies in height and density over the building. Some patches are easy and some are difficult depending on the texture. Frequently has a lot of air bubbles. Being pure cement it also seems to crack quite a bit easier than stucco which was formulated for the purpose of covering a wall. This texture is usually really sharp and the form of the texture is a result of how thin or thick the concrete was when it was sprayed along with the distance from the wall and the air pressure. Frequently the density and height of the “mini volcanoes” changes significantly over the course of the building. This makes matching the texture difficult, and each repair might require a completely different look. The person doing the patching needs to mimic these “mini volcanoes” as closely as possible by controlling the variables. All of the sprayed concrete stucco homes I’ve seen have been older.
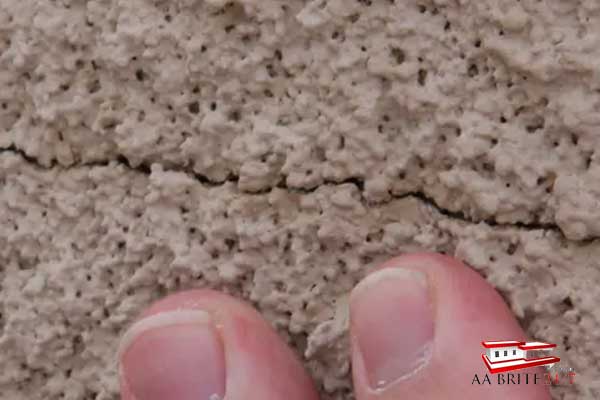
4) Spanish Lace Stucco
If the stucco texture going on my home was my choice (it’s not), we would use Spanish lace for the numerous reasons shown below instead of picking Sanded.
Advantages: Cracks less than all other kinds. Is the best for hiding defects. Seems to be stronger than other types. A popular stucco for new construction. I don’t know the specific reason why but Spanish Lace is by far the most resistant to cracking. If a sanded and Spanish lace home are next to each other and were built at the same time the Spanish Lace will almost always have considerably less cracking on it after 10 years. I suspect the added depth of the texture makes it stronger, but this is only speculation. Cracks are also more difficult to see in the Spanish lace than in the sanded.
Disadvantages: Not many other than it is not considered to be as elegant looking as sanded or smooth.
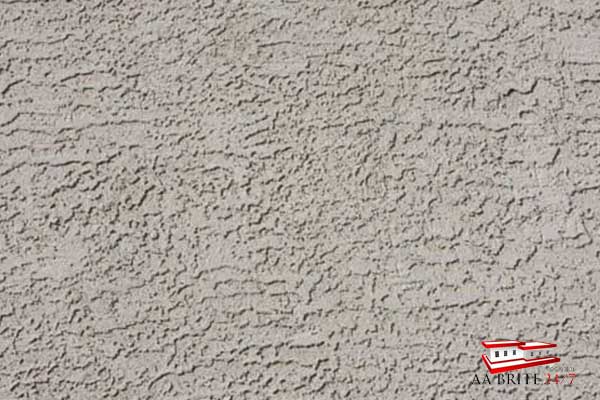
Spanish Lace is probably the most common type of stucco in the US for good reasons: 1) Its the easiest stucco to apply. By that I mean its the easiest for the builder to apply while at the same time having happy customers. 2) It can be touched up by less skilled workers. 3) Scaring and variations are less visible 4) It cracks considerably less than the other three types.
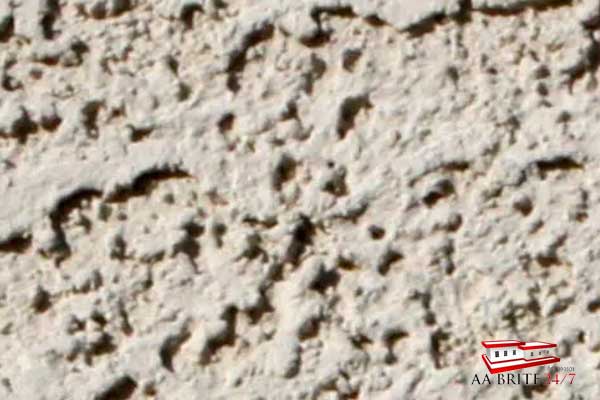
This image of Spanish lace stucco is at a higher magnification. Notice the lack of air bubbles. In my experience this is by far the most durable stucco texture. Its also the easiest to get patchwork to blend in.
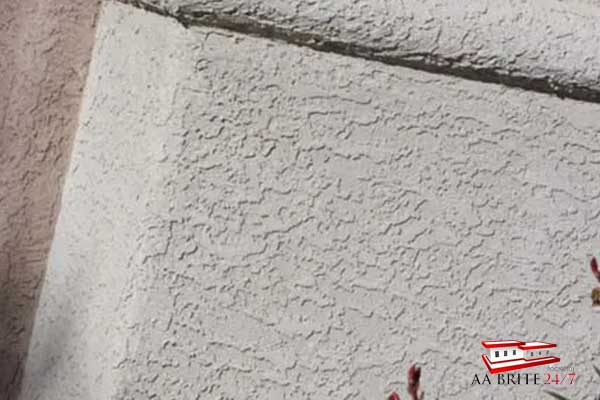
5) Tex Coating Stucco
Advantages: Applies fast. Can be sprayed on over wood and pipes.
Disadvantages: To my knowledge it hasn’t been used in the past 20 years. It flakes off in large chunks. New patches could eventually fall off since the material it’s applied to was not intended to be stuccoed.
“Tex” is our name for a common, but no longer sold or used elastomeric stuccoing paint with sand in it.
I don’t know what the material was called twenty years ago but the generic terms I’ve heard used in Tucson are “Tough Tex” and “Dex Coat” both of which are currently registered trade names of existing products, so for conversational purposes and to keep myself out of court, from here on this 15 year old sanded sprayed on plastic coating will simply be referred to as “Tex”.
Whatever Tex is or was called years ago, it’s actually an elastomeric material (plastic) similar to roof coating or really thick paint with sand mixed in it. This sandy plastic liquid was quickly sprayed from a special sprayer onto the exterior walls, fascia, trim, pipes and wires of a wood or block home. The texturing process was completed in one day by a painter. The Tex application process was much less intensive and faster than other stucco application methods since the material was more or less a paint, and applied as such. Until it went out of favor 15 or 20 years ago, Tex was put on fast, stuck to everything and looked good when new. Hurray for Tex….. Until you get to the disadvantages.
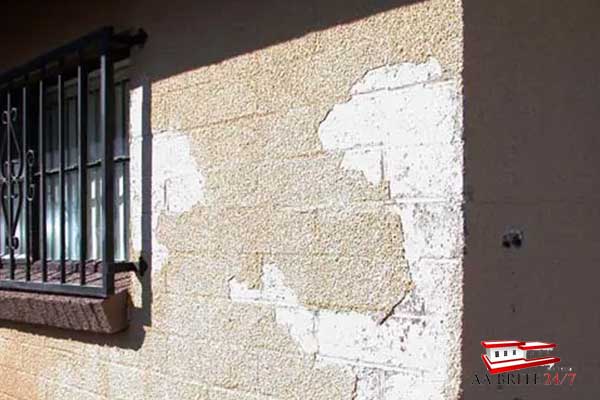
A photo of a Tex coated home I was asked to bid on. This is typical of a home with a 20 year old Tex coating on it. At one time it looked great and now its turned into a giant headache for the homeowner.
Tex doesn’t get considerably thinner like paint as it ages, instead as the coating weathers and becomes stiffer and more brittle, it will loose its grip on the surface under it. Then large thick pieces start falling off. Getting a reasonable match of the texture is not terribly difficult.
The biggest short term problem is dealing with where the edge of the new patch meets the old tex. When the painter spreads out the new sanded compound, the plastic becomes double thick on the existing old portions of old tex near the edge of the patch, and “ringworm scars” are easily formed by this small area of double thick patch. These patches range from horrible looking to slightly noticeable depending on many variables.
The skill and patience of the person doing the patch has the largest effect how the patch looks when complete. In one exceptionally rare case I had a 70 year old woman show me a patch she did and it took me almost a minute to see the witness line. She worked in her spare time on the patch the size of a t-shirt. She told me it took her 30 hours to get the edges perfect. This shows it can be done if a person is willing to put the necessary man hours into it or to pay someone to do it. Most Tex patch jobs we’ve completed were actually “paint jobs” on rental homes, and patching the tex was secondary. Our rates have ranged from $1,200 to $4,000 on these jobs. The goal – so far – has always been to get the house patched and painted without spending much larger sums of money.
Most painting contractors shy away from tex repairs because the old tex continues to come off and they don’t want to be responsible for this. We not only repair tex, but we will warranty the work for two years. Before providing a quote I’ll carefully look at the tex and determine what the different avenues are for repair.
The following photos are from a job done almost two years ago. The first two photos were taken at the time we did the job and the last photo was taken recently.
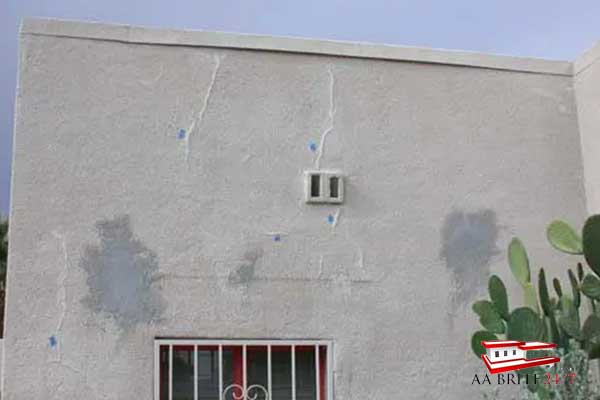
A tex coated home with the first two patches applied. Notice the scars near the pieces of blue tape. These are previous repairs and the caulk lines are visibly raised up making scars.

During the repair process. As you can see over 19 different spots were patched. This is typical with Tex coats.
The job is finished and some of the patch work is visible. I wish the patches were not visible at all, but the ringworm scarring talked about earlier is happening here. The ringworm scars could be removed with LARGE amounts of additional labor. The problem is for the number of scars needing to be patched it is cheaper and much more cost effective to re-stucco the home than it is to patch each spot perfectly.
In this case the owner wanted his home to look as good as possible for the least amount of money. Which translates into basic Tex patching and painting. Re-stuccoing this small home would cost approximately $10,000, plus the cost of priming and painting. We patched all around the home and painted it for about $1500. In other words – Patch and paint $1500 or Re-stucco and paint $11,500. Whats important to me as the owner is you as the client understand what the job will look like when we are finished BEFORE we start. If we are in agreement prior to starting then life is good for both of us.
6) Synthetic Sprayed Stucco
Advantages: Looks great and goes on fast. Is newer method.
Disadvantages: The very few that I’ve seen have lots of air bubbles when looked at closely, and when patched have to be painted four times. This is a close up view. From a distance it looks great and non-contractors wouldn’t normally notice the bubbles.
To my knowledge synthetic sprayed stuccos are produced by several different manufacturers. We don’t put it on new, so I’m unaware of all of the different properties or why certain types are used.
With regards to painting and patching, synthetic sprayed on stucco has an interesting set of characteristics.
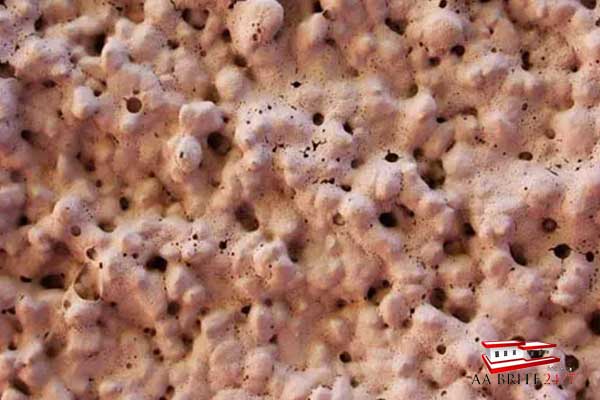
Sad to say, but most new homes are painted with what we call a “piss coat” and with synthetic stucco like the kind shown here that’s a big deal. When a thin coat of paint is put on the stucco, it doesn’t fill up the pores or air voids. When stucco in this condition is patched, most of the voids are filled in and the texture looks different. The areas with a lot of pores and air voids will look darker and rougher since the shadows from the “caves” are showing.
If a area of sprayed on synthetic stucco is patched and painted it will look completely different than the surrounding area.
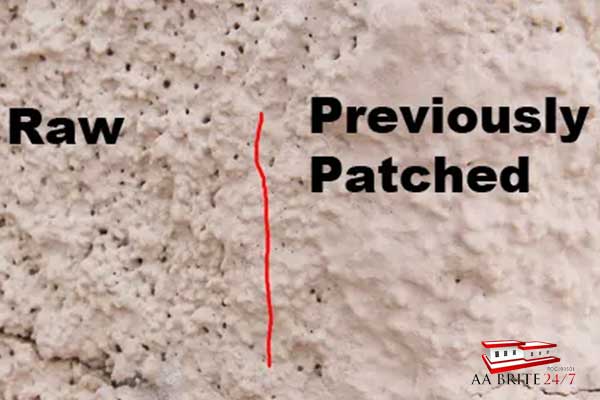
Synthetic stucco can be patched and made to look nice, doing so requires painting the entire home with a heavy coat of paint after the patching is complete. Painting after patching eliminates the two looks on one home shown in the photo above.
Once a home has been re-painted and most of the pores are filled in, future patching is much easier to do.